Dry mixed mortar is widely used in construction projects due to its convenience and efficient applicability. It consists of a combination of cement, sand, and other additives, such as cellulose ether, which plays a crucial role in ensuring the overall performance of the mortar. Specifically, cellulose ether, also known as Hydroxypropyl Methyl Cellulose (HPMC), is employed to improve the water retention capacity of dry mixed mortar, consequently enhancing its consistency and workability.
Water is crucial in the hydration process of cement, where it reacts with the cement particles to form a strong bond that ultimately hardens the mortar. However, excessive water evaporation during the drying or setting process can lead to issues such as cracking, shrinkage, and reduced strength. This is where cellulose ether comes into play. By incorporating cellulose ether into dry mixed mortar, the water retention capacity is significantly improved, effectively mitigating the negative impacts of rapid water evaporation.
In dry mixed mortar, cellulose ether acts as a water-holding agent, which allows for prolonged hydration of cement particles. This extended hydration process ensures that the mortar has sufficient time to develop optimal strength and durability. The cellulose ether molecules form a protective layer around the cement particles, reducing the water evaporation rate and maximizing water availability for hydration. As a result, the mortar consistency is improved, making it easier to spread, mold, and shape during application.
Furthermore, cellulose ether enhances the workability of dry mixed mortar. It acts as a lubricant, reducing friction between the mortar components and enabling smoother application. This improved workability not only increases productivity but also enhances the overall quality of the finished construction. The use of cellulose ether in dry mixed mortar also minimizes the risk of segregation, where the constituent materials separate during transportation or application. This ensures a homogenous mixture and consistent performance of the mortar.
Additionally, cellulose ether water retention aids in controlling the curing process of the mortar. Proper curing is crucial to achieve the desired final strength and durability of the construction material. The prolonged hydration provided by cellulose ether ensures that the mortar cures evenly and thoroughly, eliminating potential weak spots and enhancing long-term performance.
It is worth noting that the role of cellulose ether in dry mixed mortar is not limited to water retention alone. This versatile additive offers other advantages, such as improved adhesion, reduced cracking, and increased resistance to weather and chemical agents. Therefore, it is considered a crucial component in the formulation of high-quality dry mixed mortars.
In conclusion, cellulose ether water retention plays a significant role in the performance of dry mixed mortar. It enhances water availability for cement hydration, improving the mortar consistency, workability, and overall quality of the construction material. The incorporation of cellulose ether ensures prolonged hydration, reduces water evaporation, and aids in controlling the curing process. As a result, dry mixed mortar with cellulose ether offers superior performance, durability, and resilience in construction projects.
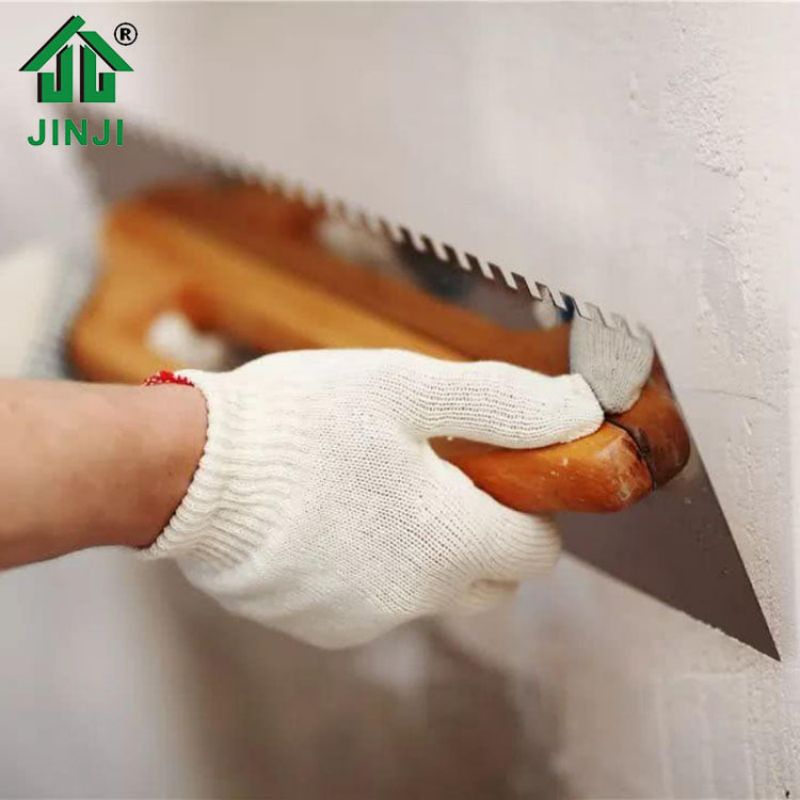
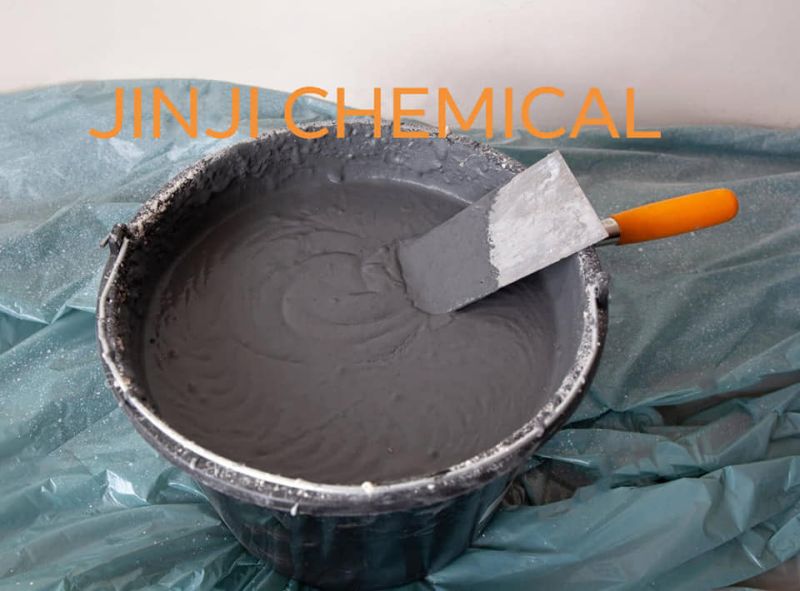
Post time: Nov-29-2023